Michael McDonagh
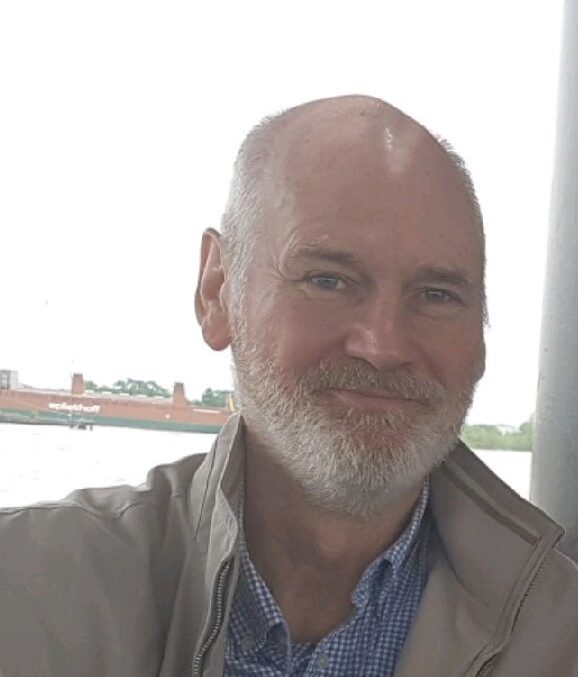
Bio
Graduated from Nottingham University with a PhD in Metallurgy and Materials science. Worked in industry in the field of battery design and manufacture, mostly in the motive power and industrial energy storage sectors. The majority of 46 year career in the industry has been at director level, responsible for all technical aspects of LA battery design, manufacturing processes and market applications.
Built 4 manufacturing plants, 3 of these were battery factories, the other was for production of molybdenum, a refractory metal. Also worked in R&D, including development of a high temperature lithium iron sulphide battery for the Trident nuclear submarine with MOD at Holton Heath UK. Was also engaged by the R@D company Ebonex as head of manufacturing for a bipolar lead acid battery.
Won 2 SMART technology awards for MF LAB batteries/connection systems for London Underground and British Rail in the early 90s.
Won an EU funded contract under the PHARE programme to supply train SLI batteries to SNCFR (Romanian rail). My company also won Welsh exporter of the year award in 1994 and consequentially, an invitation to the Queen’s Garden Party at Buckingham Palace.
In 2014 won the EU gold seal of approval for fast, low energy charging of LAB fork lift truck batteries. Awarded a Horizon 2020 grant.
Over the past 25 years, worked as an international consultant. Clients include: Zibo, Chilwee, SEC and Jinkelli in China, Microtex and Unik in India, and Shield batteries in the UK. Aso provide expert testimony in legal disputes. The two highest profile cases: Anti-Terror squad in Manchester Arena bombing and a dispute between Iran and the USA in the Court of International Justice in the Hague.
Alongside the consultancy also developing battery formation methods for flooded LAB battery manufacturers. This technology can save a typical plant around 1 million USD per annum, due to lower temperatures, 15% less energy and 20% less time c.f. conventional methods.
New LAB formation processes save manufacturers millions of USD, with lead acid battery formation energy costs composing 50% of total factory energy costs. The majority of formation programs are based on fixed Ah inputs. Little regard is given to the charging voltage despite knowing that energy is voltage-dependent. Voltage is greatly affected by two factors: the connection resistance and the method of energy input. SEM and EDX results have shown that connection resistance is linked to a complex sulphate insulating layer on the connector surface formed under conditions existing on acid-filled batteries, and acid spray during charging. Tests have shown connection resistance of manufacturers’ in-service connectors was up to 100 times greater compared to new connectors. A new formation connector design that is easier to fit and restricts acid ingress was designed. Field trials with this connector have saved battery manufacturing companies hundreds of thousands of USD by eliminating arcing damage and reducing average formation energy by 3.5% with further savings in scrap/reworked batteries. Additionally a second factor is the method of inputting energy to the battery. Highly efficient formation algorithms have been devised, saving both energy and formation time compared to manufacturer’s programmes. The algorithms rely on the kinetic lag between current input and ionic movement, to minimise the onset of the parasitic reactions of water electrolysis, gas evolution and heat. The presentation explains the thermodynamics and kinetics. Working with industrial partners, lab trials have shown that formation energy savings of 16% and time savings of 20% can be achieved for flooded SLI batteries against an industry-standard programme. The time was reduced from 10h to less than 8h, enabling a 3-shift rather than a 2-shift operation for SLI batteries. This gives a bottom-line increase of a million USD/annum for many LAB manufacturers